Induction Hardened Cutting Edges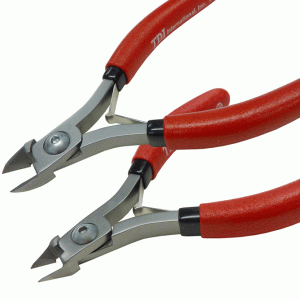
The cutting edge is the most important part of a wire cutter. Therefore preparation of the cutting edge is done with expert engineering design and outstanding workmanship for tools of the highest quality. Our high precision wire cutters, like all top quality cutting tools, have cutting edges which are induction hardened. The result is that these wire cutter have edges that are exceptionally hard. Many lower quality cutting tools are only case hardened which results in much lower cutting edge performance. What are these two hardening methods and why is induction hardening use to produce these tools?
INDUCTION HARDENING
Induction hardening is a precision process conducted entirely within the factory. A high grade, high carbon content steel is used as a base material for the tool. After machining, the tools are individually placed in the middle of an electrical coil carrying a very high frequency current. This current induces a deep heat at about 900°C in the highly localized area of the cutting edges.
The cutting edges are then rapidly cooled with a water or oil quench which immediately transforms this small, localized area into a steel structure which is exceptionally hard. In fact, the edges are so hard that they have become brittle. The tools must be tempered, by heating to around 200°C, to relieve stresses from the hardening process and to produce cutting edges which are not only hard, but hard and tough. This process achieves an overall hardness of 63-65 on the Rockwell C Scale, with a depth of 2-3mm to allow for resharpening.
Toughness is the ability to resist brittle fracture or sharp impact loads. The localized area of induction hardening can be seen on the backside of these wire cutters as light colored half moons or fans which surround the entire length of the cutting edges. This is not visible (although it is still there) on Full Flush cutting edges. These tools have undergone another careful machining process to secure this ultimate in flush cutting.
CASE HARDENING
Case hardening is usually a three step process. Fist the tool, made of low carbon steel, is surrounded by carbon to increase the carbon content on its surface, or outer case. The tools are then heated to a temperature of around 870°C, followed by an oil or water quench. This process imparts an elevated hardness to the cutting edges of the tool (as well as the rest of the tool), but this hardness is seldom over 55 on the Rockwell C Scale. Because this hardness is literally only skin deep, sharpening such tools is impossible. Why are some cutting tools made this way? Because they can be stamped from low grade material and case hardened in large, bulk quantities.
How do tools with this differently hardened edges compare? The actual number of cuts which a tool can perform before dulling is determined by the specific material being cut. Also by the force being applied. For the same material and force, tools with induction hardened cutting edges will last 5 to 10 times longer than tools which are not. Generally speaking, a resharpened induction hardened tool gets 2/3 the number of cuts it got on the first go-round. Additionally, 2/3 of that number again on the second resharpening. In comparison, a case hardened tool must be thrown away when it no longer cuts.